فولاد منگنزی Hadfield Casting یک فولاد آلیاژی است که به طور متوسط حاوی حدود ۱۳ درصد منگنز است. فولاد منگنز مقاومت زیادی در برابر ضربه و سایش دارد. منگنز توسط فولاد آلیاژی ساخته شده است و حاوی 0.8 تا 1.25٪ کربن و 11 تا 15٪ منگنز است Mangalloy یک فولاد غیر مغناطیسی منحصر به فرد است که دارای خاصیت ضد سایش شدید است. این ماده در برابر سایش بسیار مقاوم است و در شرایط ضربه تا سه برابر سختی سطح خود می رسد ، بدون افزایش شکنندگی که معمولاً با سختی همراه است . این به Mangalloy اجازه می دهد تا سختی خود را حفظ کند.
فولاد منگنز یا فولاد Hadfield (به انگلیسی: Mangalloy) یک فولاد آلیاژی است که به طور متوسط حاوی حدود ۱۳ درصد منگنز است. فولاد منگنز مقاومت زیادی در برابر ضربه و سایش دارد.
منگنز توسط فولاد آلیاژی ساخته شده است و حاوی 0.8 تا 1.25٪ کربن و 11 تا 15٪ منگنز است .[۱] Mangalloy یک فولاد غیر مغناطیسی منحصر به فرد است که دارای خاصیت ضد سایش شدید است. این ماده در برابر سایش بسیار مقاوم است و در شرایط ضربه تا سه برابر سختی سطح خود می رسد ، بدون افزایش شکنندگی که معمولاً با سختی همراه است.[۲] این به Mangalloy اجازه می دهد تا سختی خود را حفظ کند.
بیشتر فولادها حاوی 0.15 تا 0.8٪ منگنز هستند. آلیاژهای با مقاومت بالا معمولاً حاوی 1 تا 1.8٪ منگنز هستند.[۳][۴][۵] حاوی در حدود 1.5٪ منگنز ، فولاد شکننده می شود و این ویژگی تا زمانی که حاوی حدود 4 تا 5٪ از منگنز شود افزایش می یابد. در این مرحله ، فولاد در اثر ضربه چکش پودر خواهد شد. افزایش بیشتر منگنز باعث افزایش سختی و شکل پذیری می شود . در حدود 10٪ مقدار منگنز ، فولاد در صورت خنک شدن در دمای اتاق به صورت آستنیت خود باقی می ماند.[۶] هم سختی و هم انعطاف پذیری بسته به عناصر آلیاژی ، در مقدار حدود 12٪ به بالاترین نقاط خود می رسند.
اصلی ترین این عناصر آلیاژی کربن است ، زیرا افزودن منگنز به فولاد کم کربن اثر کمی دارد اما با افزایش محتوای کربن به طرز چشمگیری افزایش می یابد. فولاد Hadfield اصلی حدود 1.0٪ کربن داشت. سایر عناصر آلیاژی ممکن است شامل فلزاتی مانند نیکل و کروم باشند . اغلب به فولادهای آستنیتی به عنوان تثبیت کننده آستنیت اضافه می شود. مولیبدن و وانادیوم ؛ در فولادهای غیر آستنیتی به عنوان تثبیت کننده فریت استفاده می شود. یا حتی عناصر غیر فلزی مانند سیلیکون.
فولاد هادفیلد چیست؟
فولاد هادفیلد (به انگلیسی Hadfield steel) که با نامهای فولاد منگنز (manganese steel) و منگالوی (Mangalloy) هم شناخته میشود آلیاژی ترکیب شده از فولاد کربنی و عنصر منگنز است. حاصل این آلیاژ، افزایش خواصی مانند سختی، چقرمگی، مقاومت در برابر سایش و مقاومت در برابر ضربه میباشد. این فولاد که توسط سر رابرت ابوت هادفیلد ساخته شد آلیاژی منحصر به فرد و بسیار با دوام است که دنیای مواد صنعتی را متحول کرده است.
همانطور که گفتیم فولاد هادفیلد آلیاژی ترکیب شده از فولاد کربنی و منگنز است که 12 الی 14 درصد آن را منگنز و حدود 1 الی 1.4 درصد آن را کربن تشکیل داده است. این میزان بالای منگنز که خاصیتهای منحصر به فردی را در آن به وجود آورده است باعث شده تا این فولاد به فولاد منگنز هم معروف باشد. همچنین وجود این عنصر علاوه بر تاثیر روی قیمت فولاد هادفیلد ریزساختار آن که ساختاری آستنیتی میباشد را تثبیت کرده و باعث افزایش سختی آن میشود.
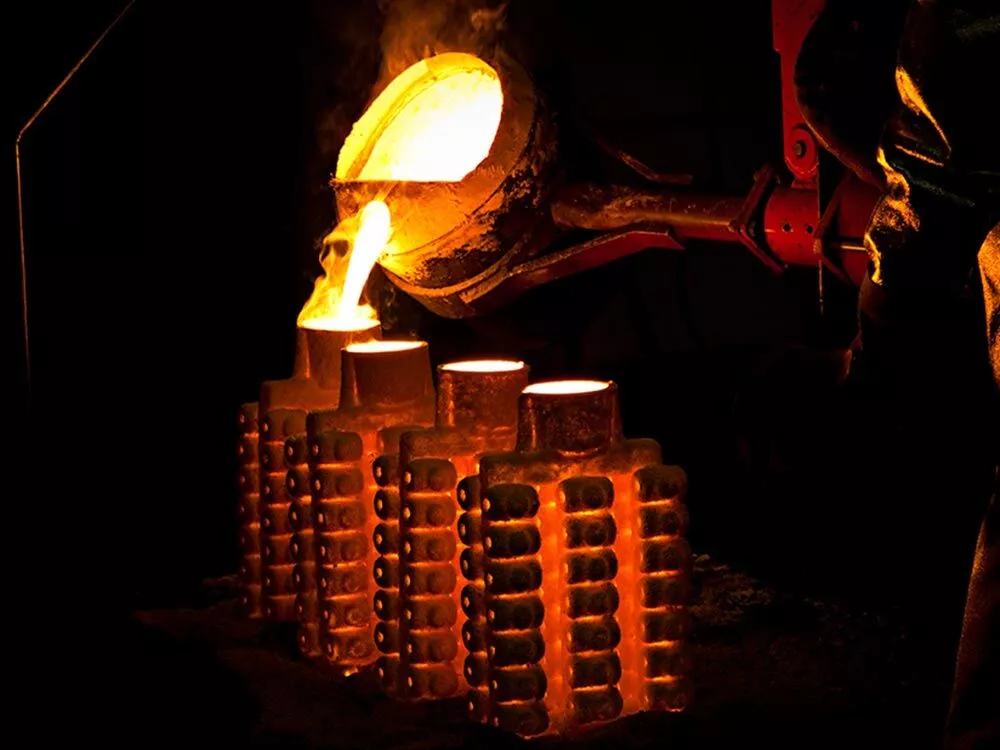
تاریخچه فولاد هادفیلد Hadfield
در اواخر قرن نوزدهم بود که متالورژیستی بریتانیایی به نام سر رابرت ابوت هادفیلد فولادی با خواص ویژه ساخت و نام آن را فولاد هادفیلد گذاشت. رابرت مطالعهی بسیار زیادی روی آلیاژهای فولادی و کاربردهای آنها داشت و همین تلاشهای بی وقفهاش بود که منجر به ساخت این ماده انقلابی شد. هادفیلد در 28 نوامبر 1858 در شفیلد انگلستان متولد شد. او راه پدرش را دنبال کرده و به تجارت فولادسازی خانوادهاش پیوست. او در همین دوران فعالیت در تجارت خانوادگی بود که به متالورژی و آلیاژهای فولاد علاقهمند شد.
در آن زمان صنایعی مثل معدن و حفاری به سرعت در حال گسترش بودند و تقاضا برای فولادهای با دوام رو به افزایش بود. در واقع آنها متقاضی توسعه فولادهایی بودند که در شرایط سخت حفاری مقاومت کنند. همین موضوع جرقهای شد تا هادفیلد به فکر ساخت آلیاژی فولادی بیفتد که توان مقاومت در برابر سایش و ضربه را داشته باشد. او آزمایشات زیادی را برای بررسی اثرات عناصر آلیاژی مختلف بر فولاد انجام داد تا اینکه اثر منگنز را مشاهده کرد. درواقع منگنز بود که باعث شد اولین قدم تولید فولاد هادفیلد برداشته شود.
هادفیلد در سال 1882 میلادی آلیاژ فولادی خود را که دارای میزان منگنزی در حدود 12 الی 14 درصد بود به ثبت رساند. او دریافت که این ترکیب میتواند با عملیاتهایی مختلف منجر به ایجاد یک زیرساختار منحصر به فرد به نام آستنیت شود. این ریز ساختار فولاد هادفیلد که یک فاز غیر مغناطیسی بود باعث افزایش سختی، استحکام، چرمگی، مقاومت در برابر سایش و مقاومت در برابر ضربه میشد. این خاصیتهای بهبود یافته باعث شدند تا فولاد منگنزی راه ورود به صنایع مختلف را پیدا کند. صنایعی مثل صنایع معدنی و راه آهن جزو اولین صنایعی بودند که این فولاد شگفتانگیز را برای قطعات و تجهیزات مختلف به کار گرفتند.
محبوبیت و موفقیت فولاد هادفیلد به سرعت از مرزهای بریتانیا هم گذشته و شهرتی جهانی پیدا کرد. مهندسان و تولیدکنندگان فولاد ارزش بسیار زیاد این آلیاژ را درک کرده و شروع به استفاده از آن در طرحها و تولیدات خود کردند. با اینکه کیفیت این فولاد به اندازهی کافی زیاد بود اما آنها به همین میزان هم بسنده نکرده و شروع به اضافه کردن مواد مختلف به آن کردند تا خواص مورد نیازشان را شخصیسازی کنند. امروزه فولاد هادفیلد در صنایعی که به سختی زیاد و مقاومت بالایی در برابر سایش نیاز دارند به طور گستردهای به کار میرود.
مقاومت فولاد منگنز
بیشتر فولادها حاوی 0.15 تا 0.8٪ منگنز هستند. آلیاژهای با مقاومت بالا معمولاً حاوی 1 تا 1.8٪ منگنز هستند. حاوی در حدود 1.5٪ منگنز ، فولاد شکننده می شود و این ویژگی تا زمانی که حاوی حدود 4 تا 5٪ از منگنز شود افزایش می یابد.
در این مرحله ، فولاد در اثر ضربه چکش پودر خواهد شد. افزایش بیشتر منگنز باعث افزایش سختی و شکل پذیری می شود.
در حدود 10٪ مقدار منگنز،فولاد در صورت خنک شدن در دمای اتاق به صورت آستنیت خود باقی می ماند.
هم سختی و هم انعطاف پذیری بسته به عناصر آلیاژی ، در مقدار حدود 12٪ به بالاترین نقاط خود می رسند.
اصلی ترین این عناصر آلیاژی کربن است ، زیرا افزودن منگنز به فولاد کم کربن اثر کمی دارد اما با افزایش محتوای کربن به طرز چشمگیری افزایش می یابد. فولاد Hadfield اصلی حدود 1.0٪ کربن داشت. سایر عناصر آلیاژی ممکن است شامل فلزاتی مانند نیکل و کروم باشند.
اغلب به فولادهای آستنیتی به عنوان تثبیت کننده آستنیت اضافه می شود. مولیبدن و وانادیوم ؛ در فولادهای غیر آستنیتی به عنوان تثبیت کننده فریت استفاده می شود. یا حتی عناصر غیر فلزی مانند سیلیکون .
منگنز دارای مقاومت در برابر عملکرد منصفانه اما استحکام کششی بسیار بالایی است ، به طور معمول در هر جایی بین 350 تا 900 مگاپاسکال (MPa) ، با کار سختی به سرعت افزایش می یابد.
برخلاف دیگر اشکال فولاد ، وقتی تا نقطه ی شکست کشیده می شود ، مواد دچار کاهش سطح مقطع نمیشوند (در ضعیف ترین نقطه کوچکتر می شوند) و بعد از هم جدا می شوند.
در عوض ، کار سختی فلزات افزایش می یابد و استحکام کششی را به سطوح بسیار بالایی افزایش می دهد ، گاهی اوقات به اندازه 2000 مگاپاسکال. این باعث می شود مواد مجاور سطح مقطع شان کوچک شود ، سخت شوند و این کار ادامه یابد تا زمانی که کل قطعه بسیار بلندتر و نازک تر شود.
کاربرد فولاد منگنز
1) ماشین آلات و تجهیزات ساختمانی: صفحه سطل، صفحه لبه جانبی، صفحه پایین سطل، تیغه و صفحه کمکی بیل مکانیکی.
2) ماشین آلات و تجهیزات ساختمانی: صفحه دندان فشار دهنده سیمان، صفحه آستر میکسر بتن، صفحه آستر حذف گرد و غبار.
3) ماشین آلات و تجهیزات معدن: صفحه آستر و تیغه سنگ شکن معدنی و سنگ.
4) سایر تجهیزات مکانیکی: آسیاب شن و ماسه، قطعات مقاوم در برابر سایش ماشین آلات مختلف بندر.
5) تجهیزات برق حرارتی: بوش آسیاب زغال سنگ، قیف زغال سنگ، لوله توزیع زغال سنگ، بوش تجهیزات تخلیه زغال سنگ.
6) سایر موارد: آسانسور، تابه آلومینیومی، قفسه های آسیاب نورد، ریل.
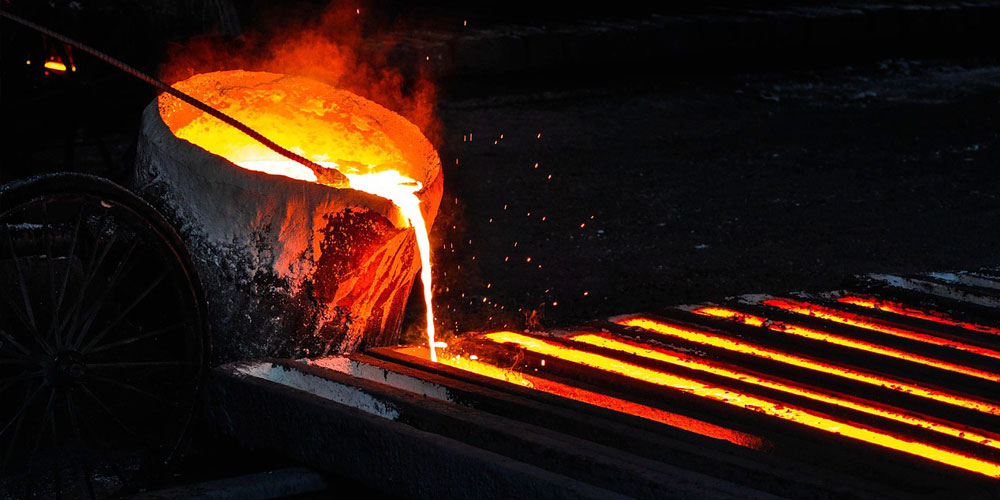
از خواص فولاد منگنزی می توان به موارد زیر اشاره نمود:
- قابلیت استفاده از گرید های مختلف فولاد منگنزی بعد از عملیات بازبخت انحلالی و کوئنچ در آب
- سخت بودن عملیات ماشین کاری بر روی قطعات تولید شده با فولاد منگنزی و نیاز به استفاده از تجهیزات و ابزار خاص برای انجام ماشین کاری
- داشتن چقرمگی بالا نسبت به فولادهای کربنی
- داشتن قابلیت آهنگری گرم در دمای 1100 درجه سانتیگراد
- فولاد منگنزی در درمای 1200 درجه سانتیگراد تحت عملیات پتک کاری از هم گسیخته می شود.
- امکان برش کاری با استفاده از برش لیزر، پلاسما و اکسی استیلن
- تمایل بالای فولاد منگنزی مذاب به اختلاط با مواد اسیدی دیرگداز
- هدایت حرارتی کم با ضریب انبساط حرارتی بالا
- تمایل بالای آستنیت نیمه پایدار به پرلیت و یا کاربید.
- از ویژگی های عناصر آلیاژی ذکر شده می توان به مورد زیر اشاره نمود:
– كربن :کم کردن تنش تسلیم فولاد با کاهش میزان کربن، کم کردن میزان تردی با کاهش میزان کربن، بروز مشکل در عملیات حرارتی با افزایش میزان کربن.
– منگنز: ایجاد تاخیر در فرایند تبدیل شدن آستنيت به فريت، افزایش میزان استحکام کششی و خاصیت چکش خواری با افزودن 10-14% منگنز، کاهش میزان طول نسبی کششی با افزودن 10% منگنز.
– سيليسيم: ارتقا ویژگی سیالیت فولاد مذاب، اکسیژن زدایی، کاهش چکش خواری و استحکام با افزودن 2.2% سیلیسیم.
– نيكل: افزایش میزان پایداری آستنیت و بهبود جوش پذیری
– كروم: کروم به میزان 1 تا 2 درصد برای افزایش تنش تسلیم و سختی به همراه کاهش چقرمگی
– موليبدن: به میزان 1 تا 2 درصد موليبدن برای افزایش تنش تسلیم و سهولت تولید قطعات با وزن بالا
– واناديوم: کاهش چقرمگی و افزایش سختی و تنش تسلیم
– تيتانيم: بهبو خواص فلز در برابر ترد شدن و ترک خوردن در خلال عملیات حرارتی و کاهش میزان چقرمگی - ريخته گري فولاد منگنزی: با توجه به مواد تشکیل دهنده موجود در ساختار فولاد منگنزی، یکی از راه های: ذوب ضایعات – اکسیداسیون – احیا (روش اول)، شارژ ضایعات فولاد منگنزی- ذوب – اکسیداسیون(روش دوم) و روش تک سرباره برای ذوب این فولاد استفاده می شود.
- طراحی قطعه: در این مرحله باید فاکتورهایی مثل نوع ماده، ضخامت، ابعاد، شکل ظاهری، کیفیت، هزینه های تولید و … را درنظر گرفت.
کاربرد فولاد هادفیلد
خواص منحصر به فرد فولاد هادفیلد باعث شده تا این فولاد در صنایع گوناگون کاربرد موثری پیدا کند. کاربردهایی که به این فولاد وابسته شده و در صورت نبودن خواص این فولاد دچار مشکل خواهند شد. در ادامه به بررسی برخی از این کاربردها خواهیم پرداخت.
صنایع معدنی
ویژگیهایی مثل چقرمگی استثنایی و مقاومت در برابر سایش باعث شدهاند تا از فولاد هادفیلد در صنعت معدن استفاده شود. از جمله کاربردهای این فولاد در معدن میتوان به استفاده از آن در بیلهای مکانیکی، سنگشکنها و قطعاتی که در معرض سایش قرار میگیرند اشاره کرد.
تجهیزات ساخت و ساز و خاکبرداری
فولاد هادفیلد علاوه بر تحمل فشارها و بارهای سنگین، مقاومت خوبی در برابر سایش از خود نشان میدهد. این ویژگیها باعث شده تا از این فولاد در تیغههای بولدوزر و گریدر و لودر استفاده شود.
راهآهن
ریلها فشار و سایش بسیار زیادی را از سوی قطارها تحمل میکنند. بنابراین باید از مادهای استفاده کنند که در برابر فشار و سایش مقاوم باشد. همانطور که میدانید فولاد منگنز مقاومت بسیار بالایی را از خود در برابر ساییدگی و بارهای سنگین نشان میدهد. به همین دلیل است که از این فولاد در ریلها، سوئیچها و سایر اجزای تحت فشار و ساییدگی راهآهن استفاده میکنند.
جمعبندی
فلزات خالص به خودی خود ویژگیها و خواص مورد نیاز در صنایع و تولیدات مختلف را ندارند. به همین منظور آنها را با عناصر و موادی دیگر مخلوط میکنند تا ویژگیهای آن را بهبود ببخشند. حاصل این کار ایجاد آلیاژهایی خواهد بود که بسته به ترکیب انجام شده خواص مورد نظر شما را پیدا کرده است. فولاد هادفیلد هم که به منگالوی یا فولاد منگنز نیز معروف میباشد یک فولاد آلیاژی است که از ترکیب آهن و کربن و منگنز تشکیل شده است.
برای ریخته گری انواع فولادهای آلیاژی در شرکت اروم ریخته گری فولادسازان آلمان آبادی از طریق فرم تماس با ما در ارتباط باشید.
بدون دیدگاه